Introduction
The demand for efficient power is increasing rapidly as digitization and electrification continue to drive productivity and environmental responsibility, respectively. The shift towards decarbonization is driving a change in energy generation, and reducing energy consumption and waste is a key part of this transition. Government mandates and regulations are playing a major role in driving these changes, with many regions requiring reduced carbon emissions and increased use of renewable energy sources.
To meet these requirements, there is a growing need for investments in electrical technologies that can improve energy efficiency in industrial applications and enable the use of renewable energy sources. New energy efficient power conversion semiconductor technologies are playing a key role in enabling advancements in wind, solar and battery conversion efficiency, while also helping to reduce energy consumption in industrial applications. This 'Electrification of Everything' is driving the development of new testing strategies for industrial and renewable energy applications that need to address the high-power capabilities of these technologies to ensure power efficiency.
Situation and Trends
Industry accounts for a significant portion of global greenhouse gas emissions, making it a critical sector to decarbonize. A shift towards renewable energy and more sustainable practices in the industrial sector will play a crucial role in achieving a more sustainable future. Today, industrial applications, whether it be in the mining of resources, manufacturing of goods or construction, account for almost 30% of the global greenhouse gas emissions, both directly and indirectly.
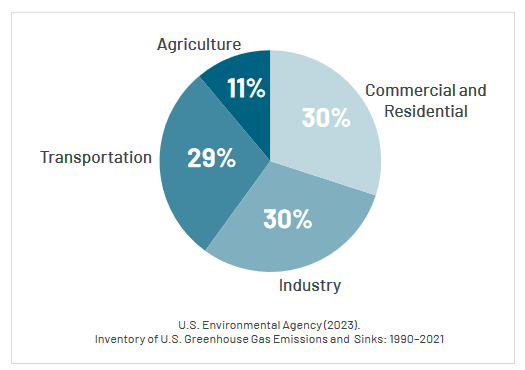
It is estimated that 51% of energy that is consumed on a global basis produce heat, mostly in the processing of materials and some manufacturing. While electrification of low- and medium-heat is possible, it may not be enough to fully decarbonize the industrial sector. While there have been efforts to electrify non-heating operations in the industrial sector, heating processes still rely heavily on fossil fuels. This is because high-temperature heat is difficult to produce without generating emissions. Therefore, new technologies and methods will be needed to address these challenges and achieve decarbonization in the industrial sector. About 50% of the fuel that industrial companies use for energy today have the potential to be electrified and decarbonized with new efficient power conversion technologies. Just a reduction in active cooling requirements alone could be a game changer. Introducing more robotics with passive cooling, fan-less solutions and motors that are of the highest efficiency will have an immediate impact on reducing emissions while reducing costs in the long term.
Moving away from fossil fuels to forms of renewable energy sources is getting more attention in the industrial sector as a means for avoiding CO2 emissions. Improvements in solar and power conversion are helping to increase overall efficiencies. Battery technologies continue to advance every year with the focus on minimizing the time between charging and increasing the level of storage capabilities on the small and very large grid scale. Fuel cell and hydrogen technologies have the potential to significantly reduce carbon emissions in industrial forms of transportation like heavy construction equipment.
Another trend that is gaining momentum and will have a significant impact on industrial manufacturing is the adoption of microgrids. A microgrid is a localized group of electricity sources and loads that can operate independently of the larger electrical grid. It can be composed of various distributed energy resources (DERs), such as solar panels, wind turbines, batteries and backup generators. Microgrids can operate in "island mode," meaning they can disconnect from the larger grid during power outages or other disruptions and continue to provide electricity to the local area. Microgrids can also be connected to the larger grid and can help to balance supply and demand, improve grid reliability and integrate renewable energy sources.
Microgrids will play a large role in the electrification of everything in industrial settings, especially at industrial manufacturing sites. At PCIM 2023, Europe’s international event on power electronics, a concept for the “DC Factory of the Future” was presented. The idea for a low-voltage DC industry grid is to offer an open system that efficiently integrates green energy, reduces resource use, optimizes energy consumption, lowers feed-in power and increases system availability(1). A DC factory would have its own power generation, whether it be solar, wind or some other source, localized energy storage facilities, machines and robotics with DC supplies, variable speed drives and robotics and various passive loads.
To achieve a decarbonized footprint in the industrial and renewable sectors, regional governments and bodies are implementing mandates and regulations. For example, the European Commission proposed the Net-Zero Industry Act in March of 2023. This regulatory act is intended to increase the competitiveness of the net-zero technology industrial base and improve the EU’s energy resilience. The act focuses on technologies including solar photovoltaic and solar thermal technologies, battery/storage technologies, heat pumps and geothermal energy technologies, grid technologies and others. The proposal sets a benchmark for the manufacturing capacity of strategic net-zero technologies to meet at least 40% of the EU’s annual deployment needs by 2030(2).
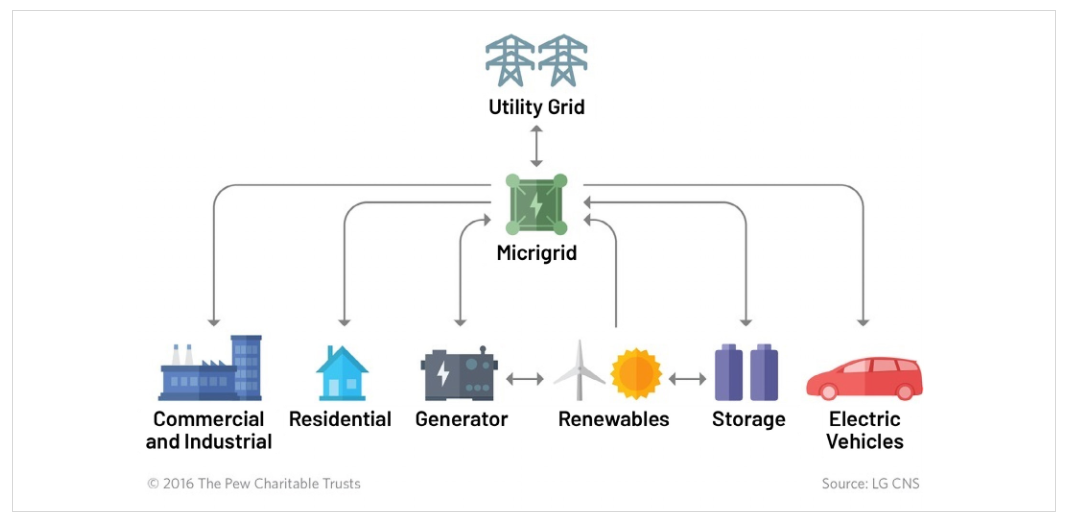
Applications to benefit from power conversion efficiency
There are numerous applications to benefit from electrification in the industrial sector.
Industrial Motors and Drives
Motors and drives are estimated to consume around 45- 50% of the world's total electricity, making them one of the largest consumers of energy globally. This is because motors and drives are used in a wide range of applications, including industrial machinery, HVAC systems, industrial transportation, heat pumps, compressors and generators. However, there are many opportunities to improve the efficiency of motors and drives, such as using highefficiency motors, optimizing motor control systems and implementing energy-efficient design practices. By doing so, we can reduce energy consumption, lower greenhouse gas emissions, save money on energy costs and even reduce audible noise.
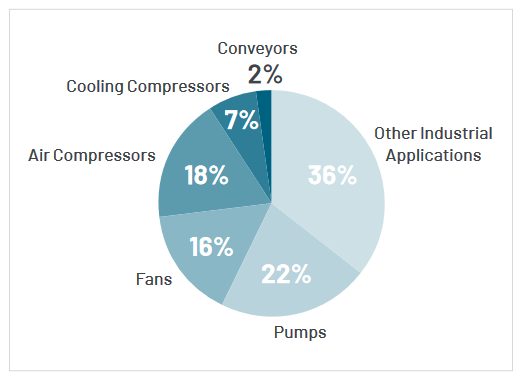
Industrial Construction Equipment
It is difficult to provide a precise estimate of the percentage of the world's energy consumed by industrial construction equipment, as it varies depending on factors such as the type of equipment and the specific industry. However, it is safe to say that industrial construction equipment does consume a significant amount of energy. This is because many construction equipment, such as cranes, excavators, and bulldozers, are powered by diesel engines, which are typically less efficient than electric motors. In addition, construction sites often require temporary power sources, such as generators, which can also contribute to energy consumption. There are opportunities to improve the efficiency of construction equipment through the use of hybrid or electric powertrains.
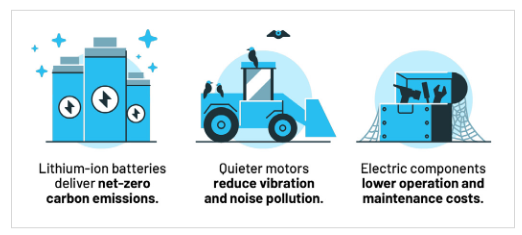
Since most industrial construction is performed in unique places, recharging electric construction equipment is quite a challenge. The grid does not always make its way to construction sites. Using alternative power sources such as solar, battery and hydrogen-based options can help address the power challenges faced by the construction industry. Portable power charging stations, in particular, can provide a reliable source of energy for remote construction sites while also reducing the strain on the local utility grid. Solar power is an especially promising option for the construction industry because it is flexible, transportable and abundant during daylight hours when construction activity is typically highest. Additionally, advancements in solar technology have made it more efficient and cost-effective, making it a viable option for powering a wide range of construction equipment and tools(3).
Handheld & Industrial Power Tools
Motor efficiency for handheld and industrial power tools can vary depending on the specific type and model of the tool. In general, however, most modern power tools use highefficiency motors that are designed to minimize energy consumption and maximize performance.
For handheld power tools such as drills, circular saws, and sanders, motor efficiency is typically measured in terms of power output and energy consumption. High-efficiency motors can deliver the same level of power as traditional motors while using less energy, resulting in lower operating costs and reduced environmental impact.
For industrial power tools such as large grinders, pumps, and compressors, motor efficiency is often measured in terms of the motor's efficiency rating, which is expressed as a percentage. High-efficiency motors for industrial applications can have efficiency ratings of up to 98%, meaning that they convert almost all of their input energy into useful work output.
By designing high-efficiency motors in both handheld and industrial power tools and improving battery storage capabilities, we can help to reduce energy consumption, lower operating costs, and improve the sustainability of the tool manufacturing and operation process.
Uninterruptable Power Systems and Backup Generators
Backup systems like UPS and generators play a crucial role in maintaining critical industrial loads when power from the grid is disrupted. Control loop technology ensures stable operation, and efficient motors can further improve the efficiency of these backup systems. Reducing switching and conduction losses can also boost system efficiency, and it's essential that the power quality of the generator is as good as the power delivered from the grid. Moreover, backup generators are vital components of a microgrid system that can be leveraged as an alternative energy source, allowing the ability to put power back on to the main grid. As the world continues to face challenges with power outages, the importance of reliable backup systems and microgrids cannot be overstated.
Solar Energy Generation, Power Inversion, and Transmission
Solar energy capability has been around for a long time. Unfortunately, the efficiency of solar panels decreases as temperature increases. This means that in hot climates, solar panels may not be able to generate as much electricity as they would in cooler climates. Solar absorption can also be a problem, especially when not all of the sunlight absorbed is converted into electricity. Some of that energy is lost as heat. Shading also limits the amount of electricity that can be generated. Silicon carbide semiconductor technology can improve the efficiency of solar panels by reducing the amount of energy lost due to heat. It can also be used in power inverters to convert the DC power generated by solar panels into AC power that can be used in homes and businesses.
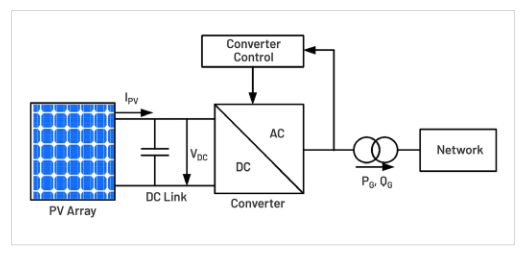
With the increasing use of solar energy, it's important to design smarter inverters that can help stabilize the grid against disruptions and ensure reliable grid operations. Because inverter-based generation can produce energy at any frequency and does not have the same inertial properties as steam-based generation, it's important for inverters to be able to respond to changes in frequency and other disruptions that occur during grid operations. This can be achieved through the use of advanced control systems that enable inverters to sense changes in the grid and adjust their output, accordingly, helping to maintain grid stability and prevent disruptions. Additionally, inverters can be designed to provide other grid services, such as reactive power compensation, voltage regulation, and power factor correction, which can help improve the overall reliability and efficiency of the grid<(4).
Why new testing challenges
Engineers continue to demand higher measurement accuracy and the ability to better understand the demands for higher power conversion efficiency. Demand for functional and reliability testing at the circuit board or subsystem level to ensure designs based on the usage of new power semiconductors like Silicon Carbide (SiC) or Gallium Nitride (GaN) is critical to ensure maximum power efficiency is delivered to the load. The drive for energy efficiency in industrial and renewable applications in particular is a significant contributor to the need for added rigor in testing and data measurements. These measurements must be robust enough to meet regulatory and certification requirements.
For example, there has been no direct way to measure the direct-quadrature-zero transformation (dq0) of a motor system for many years. This measurement typically required complex hardware, such as DC Link, LCL filters, and an FPGA. The FPGA alone required significant domain expertise for setting up the test hardware and programming the FPGA. Data logged by the FPGA was hard to interpret and visualize, and the statistics didn’t give a true representation.
Measurements and analysis on three-phase power systems are inherently more complex than on single-phase systems. Although oscilloscopes can capture voltage and current waveforms with high sample rates, further calculations are required to produce key power measurements from the data.
Control loop measurements help to characterize how a power supply system responds to changes in demand. Power systems need to respond quickly but without excessive ringing or oscillation. By measuring the actual gain and phase of a circuit over a range of frequencies, you can gain confidence in the stability of a design – greater than relying on simulation alone. Using an oscilloscope, signal source and automation software, measurements can be made quickly and presented as familiar Bode plots, making it easy to evaluate margins and compare circuit performance to models.
It's important to recognize the significant impact that electromagnetic interference (EMI) can have on the development and marketing of new power systems that rely on faster switching devices based on SiC and GaN. Compliance with EMI regulations is crucial for ensuring the reliability and safety of electrical and electronic equipment, and failure to comply can result in costly re-designs and product introduction delays. Electromagnetic compatibility (EMC) and EMI must be addressed early on in the product development process, as leaving compliance testing to the end can lead to last-minute failures, schedule delays and unplanned costs. However, having the right tools and techniques available can help prevent problems and address them quickly when they do occur. Pre-compliance testing is a common strategy for catching compliance problems early and improving the probability of a successful first pass of full EMI compliance testing. By prioritizing EMI compliance and utilizing effective testing and mitigation strategies, we can ensure the safe and reliable operation of our power systems.
Workflows are changing with an emphasis to focus on early validation of systems so that design and validation engineers can reduce time in their workflows and enable faster releases to market. One example is the solar power workflow as shown in Figure 6.
The designer today relies on dedicated hardware like solar array simulators for simulating the solar power and providing input to a grid tied inverter. A typical measurement in the workflow is the validation of Maximum Power Point Tracking (MPPT). This function requires real-world testing using an actual solar array. Designers frequently rely on digital multimeters (DMM), which do not give time domain and frequency domain waveforms, limiting the amount of analysis that can be performed.
As new engineers are entering the field to address motor & drive efficiency and delivering on the promise of delivering highly efficient renewable energy, new measurement tools are required to gain deeper insights into the performance capabilities of their designs. Tektronix is addressing many of the characterization and validation testing requirements to enable engineers to bring their products to market faster to meet the challenges of industrial and renewable electrification. The company is making significant advances in test and measurement tools to help power design engineers obtain more robust results quickly. New instrument capabilities help the engineer meet daily challenges, such as:
- Simplification of test setup to reduce measurement errors
- Reducing measurement times to extract power parameters of interest
- Increasing measurement accuracy for the design of high efficiency inverters and motors & drives
Solutions to address new testing strategies and challenges
Tektronix is addressing many of the design characterization and validation testing challenges and requirements to enable engineers to accelerate renewable power generation and moving industrial use cases to more reliance on electrical operation. Some of these applications include:
- Inverter and Motor Design Analysis
- DQ0 Controller Analysis
- Control Loop Analysis
- Switching and Conduction Loss Analysis
- Power Integrity Analysis
- EMI/EMC Compliance Testing
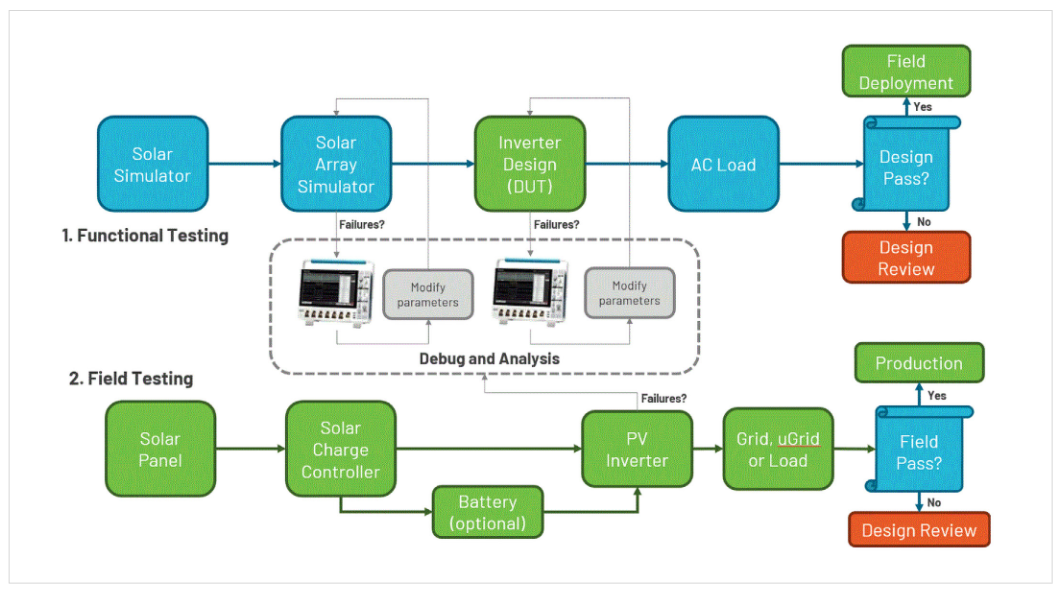
For these application areas, Tektronix offers a variety of measurement tools and software to ensure the success of the engineer, including a full line of Mixed Signal Oscilloscopes (MSO), Isolated Probes (IsoVu), Arbitrary Function Generators (AFG), Power Supplies, and Analysis Software.
The MSO oscilloscope-based three-phase solution allows capturing three-phase voltage and current waveforms with higher sample rates, longer record lengths using the HiRes acquisition mode that goes up to 16-bits and with the support of automated measurements produce key power test results. Power converters based on Pulse Width Modulation (PWM), such as variable-frequency motor drives can complicate measurements since it is very important to extract precise zero crossings for the PWM signals, thus making an oscilloscope a recommended test tool for validation and troubleshooting for motor designers. Special software, designed to automate power analysis on inverters, motors, and drives, greatly simplifies important three-phase power measurements on PWM systems and can help engineers get faster insights into their designs. The Inverter Motor Drive Analysis (IMDA) solution from Tektronix helps engineers design better and more efficient three-phase motor drive systems, taking full advantage of the advanced user interface, six or eight analog input channels, and ‘High Res’ mode (16 bits) on the 4 Series/5 Series B/6 Series B MSO. The IMDA solution provides fast, accurate, and repeatable results for electrical measurements on industrial motors and drive systems for AC induction motors, permanent magnet synchronous motors (PMSM), and brushless DC (BLDC) motors. It can be configured to measure DC to three-phase AC converters,such as those used in electric vehicles.
The MSO oscilloscope has the capability to deliver significant power integrity measurements. Key measurements important to the power engineer working on inverters include those involving Input Analysis, Harmonics, Switching Analysis, Magnetic Analysis, Frequency Response Analysis, Output Analysis, and Efficiency Analysis. Tektronix’s 4, 5 and 6 Series MSOs with their FlexChannel® inputs and innovative graphical user interfaces enables designers to test multiple test points at one go, thereby speeding up testing. The Advanced Power Measurement and Analysis option (4-PWR, 5-PWR and 6-PWR) automates the setup process for key power measurements and provides tools to evaluate test results based on norms and standards in power system design.
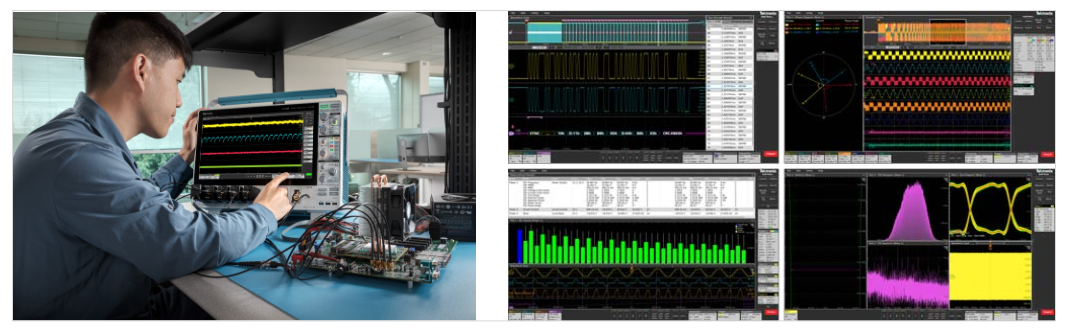
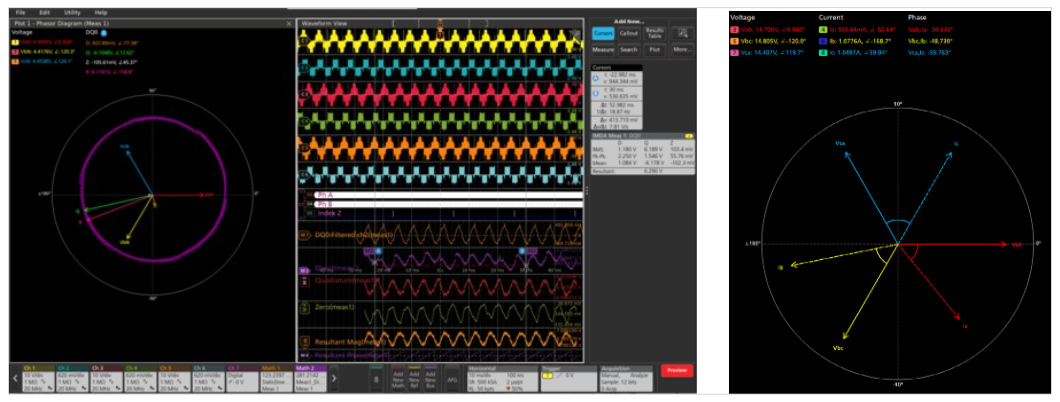
Tektronix’s 4, 5 and 6 Series MSOs. with built-in digital downconverters and Spectrum View software enable the engineer to simultaneously view both analog and spectral views of analog signals, with independent controls in each domain when performing EMI troubleshooting. Spectrum View makes oscilloscope-based frequency-domain analysis as easy as using a spectrum analyzer while retaining the ability to correlate frequency domain activity with other time-domain phenomena. Near field probes help to identify energy sources and characteristic emission profiles on a circuit board and internal cables. Energy sources generally include clock oscillators, processors, RAM, D/A or A/D converters, DC-DC converters, and other high speed switching components like SiC and GaN MOSFETs and drivers, which can produce high frequency, fast-edged signals. Current probes are used to measure high frequency cable currents. Cables are the most likely structure to radiate RF energy. Lastly, the use of a nearby antenna (typically, a 1 m test distance) is used to determine which of the harmonic signals actually radiate.
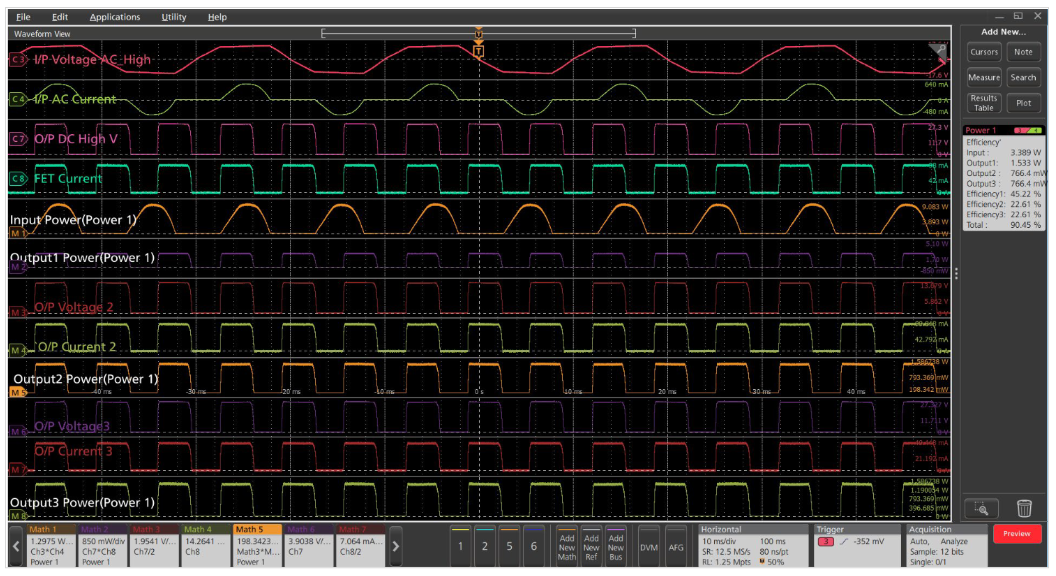
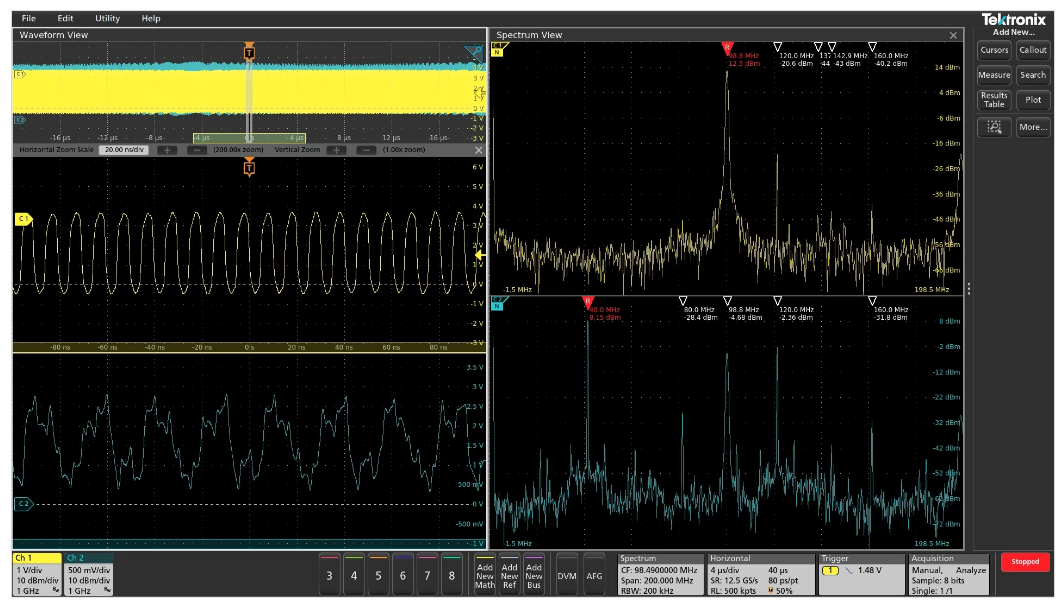
Conclusion
We live in a changing world where the management of limited energy resources has become more critical. Advances in wide bandgap semiconductor technology like Silicon Carbide and Gallium Nitride, efficient power conversion, efficient motors, and much more are enabling the development of a clean, renewable, and reliable energy ecosystem while creating new challenges for engineers. Testing tools and techniques of old will simply not be sufficient, and without the ability to measure critical values and ensure the functionality of important industrial devices, our progress can only go so far. Researchers and engineers count on Tektronix and Keithley to provide the measurement solutions to address today’s electrified ecosystem challenges and those to come.
To learn more about the applications discussed in this discussion, click on the links below.
- Making Measurements on 3-Phase Motor Drives with an Oscilloscope
- Power Supply Measurement and Analysis with 4/5/6- PWR Application Software
- Step by Step EMI Troubleshooting with 4, 5 and 6 Series MSO Oscilloscopes
Sources
- System concept DC-INDUSTRIE2, DC-INDUSTRIE Consortium, DC-INDUSTRIE & ZVEI, 29.Apr.2022
- The Net-Zero Industry Act: Accelerating the transition to climate neutrality,https://single-market-economy.ec.europa.eu/industry/sustainability/net-zeroindustry-act_en,EuropeanCommission.
- Powering Electric Construction Equipment Without Compromising the Grid,https://eepower.com/ market-insights/powering-electric-constructionequipment-without-compromising-thegrid/?utm_source=EE+Power+Members&utm_ campaign=7c98c2fd21-EMAIL_ CAMPAIGN_2023_11_02_11_03_COPY_01&utm_ medium=email&utm_term=0_-2de5c65450- %5BLIST_EMAIL_ID%5D#, EE Power, John Nieman, October 27, 2023.
- Solar Integration: Inverters and Grid Services Basics, https://www.energy.gov/eere/solar/solar-integrationinverters-and-grid-services-basics, U.S Department of Energy.
- Plugging in: What electrification can do for industry, https://www.mckinsey.com/industries/electricpower-and-natural-gas/our-insights/plugging-inwhat-electrification-can-do-for-industry, McKinsey & Company, Occo Roelofsen, Ken Somers, Eveline Speelman, and Maaike Witteveen, May 28, 2020.
- 5 Shifts Needed to Decarbonize Industry,https://www.wri.org/insights/shifts-to-decarbonize-industry, World Resources Institute, Anna Nilsson and Neelam Singh, August 1, 2023.
Find more valuable resources at TEK.COM
Copyright © Tektronix. All rights reserved. Tektronix products are covered by U.S. and foreign patents, issued and pending. Information in this publication supersedes that in all previously published material. Specification and price change privileges reserved. TEKTRONIX and TEK are registered trademarks of Tektronix, Inc. All other trade names referenced are the service marks, trademarks or registered trademarks of their respective companies.
011024 46W-74055-0